Our products
Tips:
Fibran geo
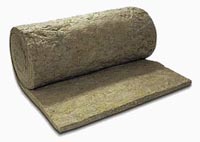
Stone wool Fibran geo ®
The advanced production technology allows FIBRAN® to offer a product with exceptional features and quality. The tight arrangement of the fibres and the permanent chemical composition, ensure standard thickness and density and even more compatibility with the rules of nature.
Attributes of Fibran geo ® stone wool
- Natural ecological product– The wool is made of minerals that derive from the earth. The production process makes the product close to nature.
- Moisture resistance – The minerals in the form of fibre are completely resistant to moist and corrosion. Also the panels, produced with special treatment, do not absorb water at all.
- Fire resistant – Thanks to its chemical attributes the stone wool does not catch on fire. The fire protection is the only one that this product has in comparison to the other insulating materials of this type and it is strongly recommended as a material for protection against fires.
- Dimensional stability - mechanical strength– The non-fire origin of the raw materials for producing the stone wool ensure stability during any type of weather conditions. Thanks to the production technology the panels have excellent additional strength, including compression and flexibility.
- Sound insulation – The structure of the fibres and their arrangement inside the stone wool makes Fibran geo ® one of the best sound insulating materials.
- Non-poison and antibacterial – The stone wool is chemically neutral; it does not contain any irritating or corrosive substances. The stone wool Fibran geo ® is not bacteria-friendly environment therefore no microorganisms or bacteria can exist in it.
Application of Fibran geo ® stone wool
- Fibran geo ® in construction
With the development of the construction technology and architecture, it becomes clear that the modern building must have:
- good thermal insulation (for saving energy and even more for protecting the environment)
- sound insulation (for normal working and living)
- protection from fire (for people and building safety)
The simple combination of the attributes that the stone wool has makes it the only solution for the above mentioned conditions.
- Fibran geo ® in the industry
Long ago had been proven that the application of the thermal insulation in the industry is of big relevance. Fibran geo ® offers one of the best solutions for these needs. The high temperatures at the industrial surroundings, in many cases the complex ecological conditions, make the Fibran geo ® stone wool irreplaceable tool in the hands of the engineers.
- Fibran geo ® in ship engineering
In this industry the very strict rules for fire protection makes the Fibran geo ® stone wool the only solution for sound and thermal insulation of the ships.
The stone wool is produced by melting the vulcanic stones
The production of the stone wool is done by melting the volcanic stones on temperature between 1500° – 1600° C from which lava is made. Afterwards the lava is spin to get the fibres, which are collected and distributed in a controlled manner to the production of homogeneous in density, panels and rolls. This somewhat simple process is possible only with the application of the highest technological achievements in production, with the purpose of ensuring that the Fibran geo ® stone wool is going to have the best quality of chemical composition and fibre dimensions.